

Core spare parts
The company uses advanced technology to produce more than
3,000 kinds of gear turbines, small precision parts, impellers,

High precision machine tool
We have strong design, manufacturing and processing capabilities and can produce a variety of general purpose mechanical equipment.

Modern production equipment
The company now has various machining centers and dozens of
CNC lathes.
-
SALES NETWORK
Changxin Machinery is in the world
The company has a number of customers, most of which are foreign-invested enterprises, state-owned enterprises and large and medium-sized private enterprises. Its foreign customers are in the United States, Britain, Germany, Japan, Israel and many other countries.
-
TECHNOLOGY
Changxin technical advantage
Our company has more than 30 years of experience in mechanical manufacturing, and has accumulated rich experience in technical and operational personnel with the production pattern of diversified products.
-
BUSINESS DOMAIN
Business field
Changxin Machinery is a professional enterprise engaged in machinery manufacturing. It is a production-oriented enterprise mainly engaged in mechanical design and processing, mold manufacturing, casting and forging.
ABOUT US
ABOUT US

质量为本 / 客户至上
Founded in 1987, Changxin Machinery Manufacturing Co., Ltd. is a manufacturing enterprise engaged in mechanical design and processing, mold manufacturing and parts forging and casting. The company is 4 kilometers north of Xushui County, 107 National Highway in the west and Jingkun Expressway in the east. It is located in Beijing, 112 kilometers from Beijing, 130 kilometers from Tianjin to the east and 135 kilometers from Shijiazhuang to the south. It is located in the center of the three major cities with convenient transportation.
CHANGXIN NEWS
CHANGXIN NEWS
What are the requirements for precision part processing?
How to choose rough materials for precision machine parts manufacturing?
Process analysis method for CNC machining parts
How is the processing of precision mechanical parts carried out?
CONTACT
CHANGXIN MACHINE


Changxin Machine Manufacturing Co.,Ltd.
Address: Xushui District, Baoding City, Hebei Province
Tel:0312-8555088
Web:http://www.changxinmachine.com
E-mail:yang@changxinmachine.com
HB1306090120161040001 冀ICP备18015840号

企业简介
长鑫机械制造有限公司位于中国河北保定,公司建于1987年,历经30余年的发展,现拥有各种CNC数控设备数十台,德国及瑞士产五轴高速加工中心5台,台湾产四轴联动龙门加工中心10台,以及日本产高精度立式和卧式加工中心等。除拥有多台配有雷尼绍探测系统的先进机床,同时可以为客户定制24小时不间断加急需求。我们的产品涉及CNC精密零件加工、污水处理格栅机、大型水闸门及汽车零部件等领域全球客户群及国内大中型城市...
核心产品
新闻中心
给我留言
填写您的电话和email信息,将有助于我们与您取得
联系,尽快解决您提出的问题
COPYRIGHT (©) 2018 保定长鑫机械制造有限公司
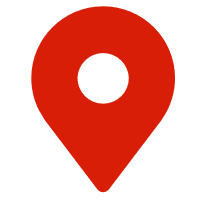
公司地址:河北保定市徐水区